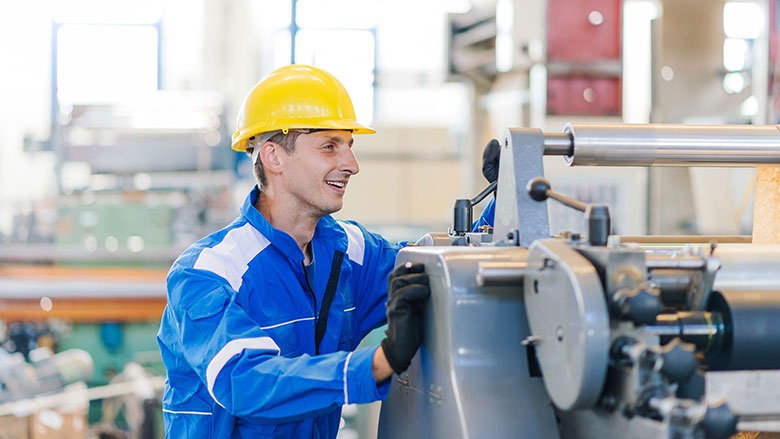
When planning and/or building an automated manufacturing system, what comes to mind first? What is the final? It is unfortunate that the last item—the security of the machines for its human operators and the vicinity in which they are located—might actually be the first in importance. While factors like cost-effectiveness and successful production line layouts are undoubtedly vital for the seamless operation of an automated system, what matters most is that it shouldn’t endanger human life or health.
Machine safety guards are an essential point of contact between the operator and the machine, and a well-thought-out design that includes them from the outset will help to maximize performance. More than was previously thought necessary, the ergonomics of a machine are now also taken into account for the long-term health and sanity of the operator. Future harmful incidents are more carefully considered. Safety barriers and sensors must also be taken into consideration as a crucial component of any design strategy in order to ensure that no one unintentionally wanders into a dangerous region of machine operation.
How Machinery Can Cause Injuries?
Numerous injuries can be caused by moving machinery like Bearing cage LM Guide SRS
(รังลูกปืน LM Guide SRS, which is a term in Thai):
- Machinery moving parts or projectiles can strike and damage people. Additionally, human parts may become entangled with or caught between pulley drives, belts, and rollers.
- Sharp points or edges can stab or penetrate the skin, whereas rough surfaces can create friction or abrasion. Sharp edges can also cause cuts and ripping injuries.
- People can be crushed by moving parts, by moving parts past one another, by moving parts into a stationary part of the machine, a wall, or another object.
What Should I Do?
Before Beginning
You should consider the potential risks and how to control them before using any machine. Thus, you ought to take the following actions:
- Verify that the machine is functional, has all necessary protections, and is defect-free. Guards, interlocks, light guards, pressure-sensitive mats, two-hand controls, and other devices fall under the umbrella term “safeguarding.” The provider is required by law to offer the necessary protections and notify customers of any dangers (sometimes known as “residual risks”) that users must be informed of and handle because they cannot be planned out.
- Create a secure workflow for maintaining and operating the machine.
- When performing maintenance, it may be necessary to evaluate important features where deterioration poses a risk. Make sure the safe system of work includes the residual hazards that the manufacturer highlighted in the information/instructions that came with the machine.
- Make sure all static machines are stable and installed correctly (usually fixed down).
- Select the appropriate machine for the work, and avoid placing it in a dangerous area where clients or visitors might be exposed.