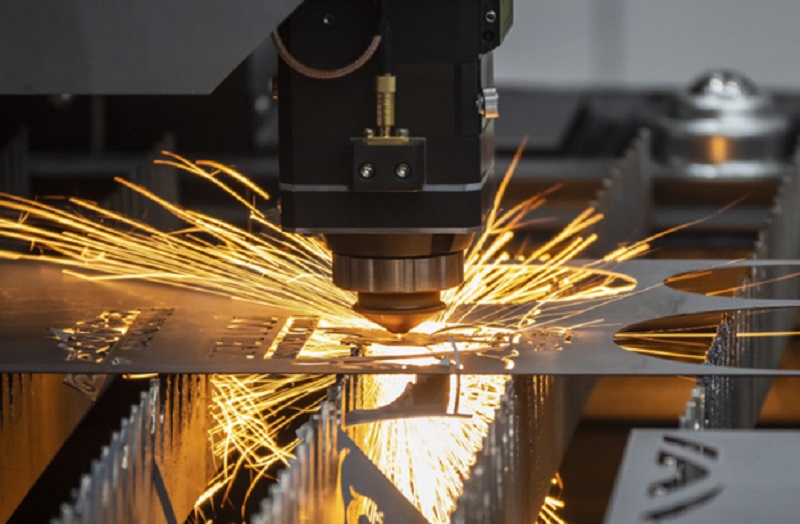
In today’s rapidly evolving world of manufacturing and fabrication, the demand for efficiency, accuracy, and cleanliness has never been more urgent. One method that has grown increasingly popular due to its reliability and consistent results is precision copper laser cutting. Known for delivering clean edges and sharp detailing, this advanced process is changing how copper components are shaped and utilised across industries.
Copper, with its superior thermal and electrical conductivity, has long been a preferred material for a variety of applications, from electrical components to decorative features. However, its softness and high reflectivity have posed challenges for conventional cutting methods. This is where laser cutting enters the picture, offering a solution that blends precision, speed, and flexibility into one streamlined process.
A Modern Solution for Intricate Designs and High-Volume Output
Manufacturers and fabricators often face the dilemma of producing complex designs quickly without compromising quality. Traditional methods involving saws, blades, or mechanical punches may struggle with consistency, especially when dealing with intricate patterns or thin sheets. Precision copper laser cutting resolves this challenge by using focused beams of light to slice through copper with unmatched exactness.
Thanks to the non-contact nature of this process, there’s minimal wear on the cutting tools, which also translates to lower maintenance costs and higher durability. This means more projects can be completed in less time, without the common hiccups associated with mechanical wear and tear.
Why Copper Demands a Special Approach
While laser cutting has been widely used for a range of metals, copper requires a specific level of control due to its reflective surface. Improper handling can lead to beam reflection, risking equipment damage or inefficient cutting. Today’s high-tech laser systems come equipped with features that can mitigate these issues, making it possible to process copper safely and effectively.
This tailored approach is particularly beneficial for industries where the reliability of copper components is non-negotiable. From telecommunications and energy infrastructure to electronics and art installations, the need for flawless copper pieces continues to grow. Laser cutting allows these sectors to achieve high-quality outputs with precision that manual methods simply can’t match.
Enhancing Productivity without Compromising Detail
The beauty of precision copper laser cutting lies not only in its accuracy but also in its ability to handle high production volumes without sacrificing detail. Whether it’s a batch of electrical contacts or ornate architectural accents, the final product comes out uniform, sharp-edged, and free from the distortions often caused by other cutting techniques.
Furthermore, the process reduces the need for secondary finishing. The smooth, burr-free edges reduce the risk of errors and rework, allowing businesses to move swiftly from production to assembly. This efficiency not only improves turnaround time but also enhances overall project quality and consistency.
Supporting Sustainability and Cleaner Operations
In an age where environmental considerations are more critical than ever, many manufacturers are seeking methods that reduce material waste and energy consumption. Precision copper laser cutting answers this call by producing minimal scrap and eliminating the need for coolants or lubricants. The accuracy of the cut also means there’s less likelihood of rejected parts, making the entire workflow more sustainable.
Moreover, the process is considerably quieter and cleaner than many traditional cutting methods. This creates a safer, more comfortable environment for operators while also minimising the impact on surrounding areas.
A Clear Investment in Quality and Reliability
Choosing laser cutting for copper is not just about keeping up with technological trends; it’s a commitment to delivering better products with more consistent results. Companies that adopt this technique often find themselves better equipped to handle complex orders, meet tight deadlines, and offer innovative designs that were previously difficult or costly to achieve.
As industries continue to evolve, staying competitive requires embracing methods that combine speed with accuracy and sustainability. Copper laser cutting does just that—bringing craftsmanship and modern engineering together in a way that benefits both producers and end-users.
Final Thoughts
From intricate shapes to mass production, the application of precision copper laser cutting is proving to be a game-changer in modern fabrication. It offers a reliable, clean, and highly accurate way to cut copper components for countless uses. As more businesses turn to advanced tools to meet rising demand, this method stands out as a smart, forward-thinking choice.
Whether you’re looking to enhance quality, boost efficiency, or reduce waste, embracing precision laser cutting can help position your work at the forefront of modern metalworking.